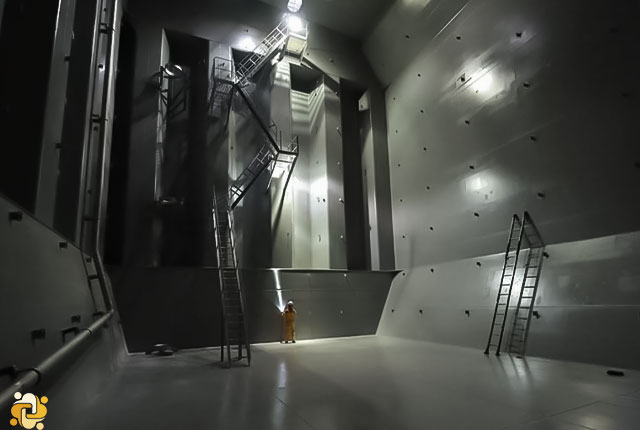
Corrosion protection of cargo oil tanks of crude oil tankers
2023-03-07 21:47
Introduction
Crude oil is a complex mixture of substances at varying ratios and in most cases contains at least some salt water. Even after desalination some of this brine remains dissolved in the crude and gradually sinks to the bottom of the cargo oil tank during transport. The corrosive nature of salt, along with microorganisms and other aggressive substances contained in the cargo oil, causes rust, most notably in the form of pitting, which are cavities in the steel that deepen over time.
Regarding above and based on the SOLAS Reg.II-1/3-11 (adopted by Res.MSC.291(87)), all crude oil tankers of 5,000 tones deadweight and above:
- for which the building contract is placed on or after 1 January 2013; or
- in the absence of a building contract, the keels of which are laid or which are at a similar stage of construction on or after 1 July 2013; or
- the delivery of which is on or after 1 January 2016
shall be constructed according below requirements:
- To be coated during the construction of the ship in accordance with 'the Performance standard for protective coatings for cargo oil tanks of crude oil tankers (Res.MSC.288(87))' (refer to 'the Application of Performance standard for protective coatings for cargo oil tanks of crude oil tankers (IACS UI SC 259/Corr.1) or
- To be protected by alternative means of corrosion protection or utilization of corrosion resistance material to maintain required structural integrity for 25 years in accordance with 'the Performance standard for alternative means of corrosion protection for cargo oil tanks of crude oil tankers (Res.MSC.289(87))'.
The Administration may exempt a crude oil tanker from the requirements of this regulation, according the following situations:
- Using of novel prototype alternatives to the coating system specified in above paragraph, for testing, provided they are subject to suitable controls, regular assessment and acknowledgement of the need for immediate remedial action if the system fails or is shown to be failing. Such exemption shall be recorded on an exemption certificate.
- If the ship is built to be engaged solely in the carriage of cargoes and cargo handling operations not causing corrosion*. Such exemption and conditions for which it is granted shall be recorded on an exemption certificate.
* Refer to Guidelines on procedures for in-service maintenance and repair of coating systems for cargo oil tanks of crude oil tankers (MSC.1/Circ.1399) and Guidelines on exemptions for crude oil tankers solely engaged in the carriage of cargoes and cargo-handling operations not causing corrosion (MSC.1/Circ.1421).
Protective coatings for cargo oil tanks of crude oil tankers
Resolution MSC. 288(87) provides technical requirements for the minimum standard for protective coatings to be applied in cargo oil tanks during the construction of new crude oil tankers. Specification of the cargo oil tank coating system applied, record of the shipyard's and ship-owner's coating work, detailed criteria for coating selection, job specifications, inspection, maintenance and repair shall be included in a document called “Coating Technical File”.
The Coating Technical File shall contain at least the following items relating to this Standard and shall be delivered by the shipyard at new ship construction stage:
- Copy of Statement of Compliance or Type Approval Certificate;
- Copy of Technical Data Sheet, including:
2.1. product name and identification mark and/or number;
2.2. materials, components and composition of the coating system, colours;
2.3. minimum and maximum dry film thickness;
2.4. application methods, tools and/or machines;
2.5. condition of surface to be coated (de-rusting grade, cleanness, profile, etc.); and
2.6. environmental limitations (temperature and humidity);
- Shipyard work records of coating application, including:
3.1. applied actual areas (in square metres) of coating in each cargo oil tank;
3.2. applied coating system;
3.3. time of coating, thickness, number of layers, etc.;
3.4. ambient conditions during coating; and
3.5. details of surface preparation;
- Procedures for inspection and repair of coating system during ship construction;
- Coating log issued by the coating inspector – stating that the coating was applied in accordance with the specifications to the satisfaction of the coating supplier representative and specifying deviations from the specifications;
- Shipyard's verified inspection report, including:
6.1. completion date of inspection;
6.2. result of inspection;
6.3. remarks (if given); and
6.4. inspector signature; and
- Procedures for in-service maintenance and repair of coating systems.
In-service maintenance and repair activities shall be recorded in the Coating Technical File in accordance with the relevant section of the Guidelines for coating maintenance and repair.
Finally, The Coating Technical File shall be kept on board and maintained throughout the life of the ship.
Alternative means of corrosion protection or utilization of corrosion resistance material
Corrosion-resistant steel - a proven alternative approach
Alternative means is a means that is not a utilization of protective coating applied according to the Performance standard for protective coating for cargo oil tanks of crude oil tankers.
Documents and information of alternative means stipulated in below shall be documented in the Technical File and it shall be verified by the Administration. The Technical File shall be kept on board and maintained throughout the life of the ship.
The mentioned document shall contain at least the following items relating to this standard and shall be delivered by the shipyard at new ship construction stage:
- copy of a Type Approval Certificate;
- technical data, including:
2.1. approved welding methods and welding consumables; and
2.2. repairing methods recommended by the manufacturer (if any); and
- records of the application, including:
3.1. applied actual space and area of each compartment; and
3.2. applied product and its thickness.
In-service maintenance, repair and renewal activities shall be recorded in the Technical File.
Corrosion resistant steels
These well-known facts prompted three Japanese steel manufacturers – JFE Steel Corporation, Nippon Steel Corporation and Kobe Steel, Ltd. – to submit a proposal to IMO to accept the use of corrosion-resistant steels as an alternative method of preventing corrosion in crude oil tanks. Following thorough discussion, IMO issued its new 'Performance Standard for Alternative Means of Corrosion Protection for Cargo Oil Tanks of Crude Oil Tankers' as an extension of the Performance Standards for Protective Coatings (PSPC) in 2010.
Research performed over a ten-year period by JFE Steel Corporation in a crude oil tanker delivered in 2008 confirmed that the corrosion-resistant steel dramatically reduced both pitting corrosion and general surface corrosion compared to uncoated conventional steel. Various other vessels featuring cargo tanks fitted with these advanced steels have been in operation since the new IMO PSPC standard came into effect and have demonstrated vastly improved corrosion resistance. The technology can thus be considered as validated.
Corrosive environment in crude oil tankers
DNV GL has since revised its relevant ship construction rules to incorporate corrosion-resistant steels for cargo tanks, and recently added the new classifier “CA” (for “corrosion protection by alternate means”) to its existing corrosion protection class notation. Announced in July 2020, the new notation COAT-PSPC(CA) confirms a ship’s compliance with the corrosion protection requirements for cargo oil tanks of crude oil tankers, by application of approved corrosion-resistant steel grades in one of the following areas of a cargo tank:
- Lower surface of the strength deck and surrounding structures (RCU)
- Upper surface of the inner bottom plating and surrounding structures (RCB)
- Both the strength deck and the inner bottom plating (RCW)
Besides using the approved steel grades, the notation also implies the use of appropriate, approved welding consumables to join the plates. Compliance with both requirements must be substantiated by submitting specific documentation.
Eliminating the cost of coating
Opting for corrosion-resistant steels in the corrosion-prone areas of crude oil tanks offers various benefits to owners and charterers as well as shipyards. One example is to eliminate the cost of coating and shortening the time it takes to complete a new-build in the yard.
Furthermore, no coatings need to be reapplied to the relevant tank wall areas over the lifetime of the vessel since the IMO performance standard assumes a useful life of 25 years of the cargo oil tank (COT) steel until its thickness is reduced beyond acceptable levels. Owners who choose this class notation can demonstrate to cargo owners that their crude oil tankers have a lower risk of tank bottom or wall failure, cargo loss and environmental pollution, thereby enhancing confidence in their ships.