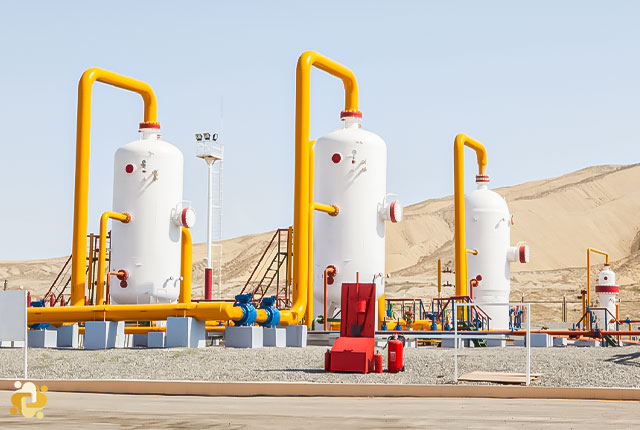
Leak Detection for Energy Transition (E-RTTM)
2023-02-07 18:30
Introduction
With a shift from fossil-based systems of energy production and consumption to renewable energy sources also comes a shift for the transportation. This is also true for pipeline leak detection systems. To guarantee the safe and efficient monitoring of the pipelines, leak detection systems must be adapted to the new requirements coming with the shift.
While there are pipelines transporting 100% hydrogen, there are others transporting a blend of hydrogen with natural gas. In carbon capture applications, the captured CO2 is transported to sites where the CO2 is stored or utilized. This CO2 can be transported as gas, liquid or in supercritical state. As a result, the leak detection system needs to be able to work with these different mixtures and phases. For classical leak detection systems this is often a problem.
Negative Pressure Wave leak detection systems are affected due to damping in gas. Classical statistical systems are affected due to compressibility and line pack changes. This leads to long detection times or high thresholds. The systems will react with a loss of sensitivity or in the worst case with false alarms.
Different mixtures and phases in the same pipeline are a typical application for Real-Time Transient Model technology (RTTM) based systems, which try to consider all blends of different products and pipeline properties in its calculations. However, if the fluid cannot be accurately modelled by the system this leads to false results. Unforeseen operating conditions will also lead to false alarms. The Extended Real-Time Transient Model technology (E-RTTM) can compensate for these disadvantages. The following chapter shows how the technology works.
Principle of E-RTTM (Extended Real-Time Transient Model)
E-RTTM is a leading technology for continuous internal monitoring of pipelines. It was developed by KROHNE, a manufacturer of measuring technology and established supplier of systems for the pipeline industry.
The E-RTTM introduced here is the basis of the Pipe Patrol leak detection system by KROHNE. With more than 35 years of experience with the technology and over 430 installations, the system has proven itself in monitoring liquid and gas pipelines (including liquefied gas and supercritical products) and meets all the requirements of TRFL and API RP 1130. Requirements of recent publications like API 1175 are also met. Next to the vertical combination of the virtual pipeline with pattern recognition, a horizontal approach combining different API 1130 methods into one system is present.
Figure 1: Basic functional principle of E-RTTM
E-RTTM extends a feature generation module with leak signature analysis using leak pattern detection:
an E-RTTM leak detection system creates a virtual image of a pipeline based on measured data. Measured values from flow, temperature and pressure sensors installed at the inlet and outlet of the pipeline and along the pipeline in places such as pump and valve stations are crucial. The flow, pressure, temperature and density at each point along the virtual pipeline are calculated from the measured pressure and temperature values.
The model compares the calculated flow values with the actual values from the flow meters. If the model detects a flow discrepancy, the leak signature analysis module then determines whether it was caused by an instrument error, a gradual leak or a sudden leak.
The Signature Analysis also makes the system less sensitive against inaccuracies in RTTM calculations, for example caused by blends of different products. Thus challenging pipeline conditions, product parameters or mixtures, e.g. hydrogen blends, that lead to these inaccuracies become less important. In Pipe Patrol, the RTTM is only used for filtering purposes, but leaks are detected by pattern recognition techniques.
E-RTTM provides a high degree of sensitivity and quick leak detection with real-time comparison of existing measuring results against leak signatures, which are stored in a database. Comparing of measured values with the leak signatures is also critical to the reliability because it provides a high degree of protection from false alarms.
E-RTTM-based leak detection systems can handle transient conditions that are not recognized by less sophisticated internal leak detection systems. An E-RTTM based leak detection system works with dynamic values, which also boosts robustness, the system becomes independent of the absolute accuracy of the virtual pipeline. It can adapt automatically and very quickly to changes in the operating conditions such as sensor failure, communications failure, a valve closing or a product change in the pipeline.
Practical examples are given below.
Smallest detectable leak rates are typically 0.5% and below. Leak detection time in seconds, confirmation within minutes It has an exceptionally low false alarm rate due to onsite optimization.
Due to the pattern recognition process it detects smallest leaks reliably and delivers repeatable results over a long period. Leak size information is statistically refined and the leak localization is best-in-class by Gradient Intersection Method and Extended - Negative Pressure Wave Method.
Leak Detection System for Hydrogen
The leak detection system was installed on a hydrogen Power-to-Gas project in Germany which was the world’s first demonstration plant for storing wind energy in the natural gas grid. The plant stores electricity generated by wind turbines. Around 360 Sm³/h of hydrogen is generated by means of electrolysis and fed via a 1.6 km hydrogen pipeline into the gas grid.
As the leading leak detection system provider in Germany, KROHNE had been recommended by an independent 3rd party authority to be the supplier for the leak detection system which monitors the hydrogen pipeline connecting the alkaline electrolysis with the natural gas grid. The E-RTTM technology was selected due to its ability to measure a supercritical product even in small leak quantities and the model was adapted to the hydrogen properties. This was the first Power to Gas Application equipped with a Pipe Patrol leak detection system in 2013. Since then, Pipe Patrol has been installed on several hydrogen pipelines.
With all pipelines, a leak test was done under 3rd party review of TÜV, resulting in a swift leak alarm from Pipe Patrol. Since beginning of operation, the system has secured the transport of over 10 million kWh of hydrogen (“Wind Gas”) fed into the grid.
Leak Detection System for Carbon Capture
The second application takes place in Western Australia: natural gas from the Gorgon gas field contains around 14% naturally occurring CO2. Prior to converting the natural gas to LNG by cooling it to -162°C / -259.6°F, the CO2 is removed. To minimize the environmental footprint, the separated CO2 is not vented but injected in a storage formation.
A 7 km long underground pipeline transports the CO2 from the LNG liquefaction plant to the CO2 injection wells.
The CO2 is transported in supercritical phase at elevated pressures. The underground pipeline has a diameter of 300 mm / 12”. Three compressor modules feed CO2 in the pipeline that transports it to nine injection wells at three drill centers. The measurement requirement for this project was to provide a pipeline leak detection system that provides timely and accurate leak information for the three pipeline-segments between the LNG plant and drill-centers.
KROHNE provided the E-RTTM based leak detection system. Based on flow, pressure and temperature measurement at inlet and outlet of the pipeline, and a digital twin of the pipeline, the system calculates the flow, pressure and temperature at any given position in the pipeline, using Real Time Transient Modelling.
In case calculated flow, pressure and temperature start to deviate from actual measured value, a proprietary algorithm (pattern recognition) developed to avoid false alarms, is used to distinguish between a sensor drift and a true leak. The project involved unique conditions, such as the specific thermos physical properties of CO2 in the supercritical phase and the flow measurements done by orifice plates with a limited range ability.
A pipeline leak detection system based on E-RTTM supports the safe management of the CO2 transport pipeline’s operations. In case of a leak, whether spontaneous or a small creeping leak, Pipe Patrol will alarm the customer accordingly.
Reference:
- Pipeline Technology Journal