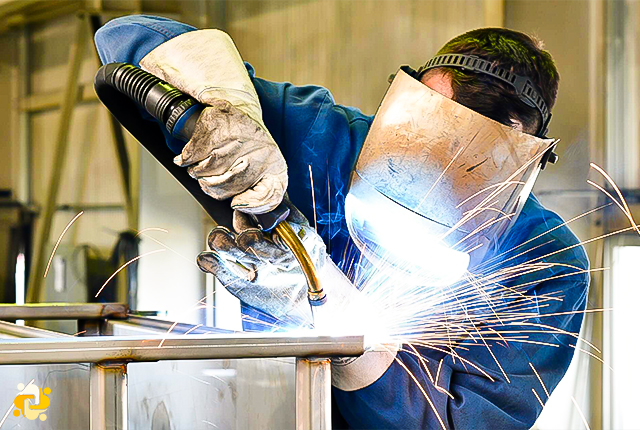
TIG Welding (GTAW) Process
2022-04-30 22:58
Gas tungsten arc welding (GTAW) is a process in which the joining of metals is produced by heating therewith an arc between a tungsten (non-consumable) electrode and the work with a TIG welding machine.
A shielding gas is used, normally argon.
 Process-a.jpg)
A number of tungsten alloys have been standardized by the International Organization for Standardization and the American Welding Society in ISO 6848 and AWS A5.12, respectively, for use in GTAW electrodes, and are summarized in the adjacent table.
- Pure tungsten electrodes (classified as WP or EWP) are general purpose and low cost electrodes. They have poor heat resistance and electron emission. They find limited use in AC welding of e.g. magnesium and aluminum.
- Thorium oxide (or thoria) alloy electrodes offer excellent arc performance and starting, making them popular general purpose electrodes. However, thorium is somewhat radioactive, making inhalation of vapors and dust a health risk, and disposal an environmental risk.
- Cerium oxide (or ceria) as an alloying element improves arc stability and ease of starting while decreasing burn-off. Cerium addition is not as effective as thorium but works well, and cerium is not radioactive.
- An alloy of lanthanum oxide (or lanthana) has a similar effect as cerium, and is also not radioactive.
- Electrodes containing zirconium oxide (or zirconia) increase the current capacity while improving arc stability and starting while also increasing electrode life
ISO Class | ISO Color | AWS Class | AWS Color | Alloy |
---|---|---|---|---|
WP | Green | EWP | Green | None |
WC20 | Gray | EWCe-2 | Orange | ~2% CeO2 |
WL10 | Black | EWLa-1 | Black | ~1% La2O3 |
WL15 | Gold | EWLa-1.5 | Gold | ~1.5% La2O3 |
WL20 | Sky-blue | EWLa-2 | Blue | ~2% La2O3 |
WT10 | Yellow | EWTh-1 | Yellow | ~1% ThO2 |
WT20 | Red | EWTh-2 | Red | ~2% ThO2 |
WT30 | Violet | ~3% ThO2 | ||
WT40 | Orange | ~4% ThO2 | ||
WY20 | Blue | ~2% Y2O3 | ||
WZ3 | Brown | EWZr-1 | Brown | ~0.3% ZrO2 |
WZ8 | White | ~0.8% ZrO2 |
The heated weld zone, molten metal, and tungsten electrode are shielded from the atmosphere by a covering of inert gas fed through the electrode holder.
GTAW Gasses
- 100% Argon (most common, coolest)
- 75% Argon/25% Helium
- 75% Helium/25% Argon (hottest gas, higher % of helium can result in arc starting issues)
- 100% Helium (hard to start arc, very hot.)
Different shielding gases and their effects are mentioned in the table below.
Characteristics | Argon | Helium | Argon + Helium |
---|---|---|---|
Travel speed | Reduced travel speed | Faster travel speed | Depends on mixture, more helium – more travel speed |
Penetration | Reduced penetration | Increased penetration | Depends on mixture, more helium – improved penetration |
Cleaning | Good cleaning action | Less cleaning action | Cleaning properties closer to argon |
Arc starting | Easier arc starting | Difficult arc starting | Depends on mixture, more argon – more easier arc starting |
Arc stability | Good arc stability | Lower arc stability at lower current | Depends on mixture, more argon – more stable arc |
Arc voltage | Lower arc voltage | Higher arc voltage | Moderate arc voltage |
Flow rate | Lower flow rate | Higher flow rate | Higher flow rate than argon |
Cost | Lower cost and greater availability | Higher cost than argon | Comparatively higher cost due to argon |
Filler metal may or may not be added. A weld is made by applying the arc so that the touching work piece and filler metal are melted and joined as the weld metal solidifies.
his process is similar to other arc welding processes in that the heat is generated by an arc between a non-consumable electrode and the work piece, but the equipment and electrode type distinguish it from other arc welding processes.
Advantages and Disadvantages
Advantages
- Works on almost all types of metals with higher melting points. Gas tungsten arc welding is the most popular method for welding aluminum stainless steels, and nickel-base alloys. It is generally not used for the very low melting metals such as solders, or lead, tin, or zinc alloys. It is especially useful for joining aluminum and magnesium which form refractory oxides, and also for the reactive metals like titanium and zirconium, which dissolve oxygen and nitrogen and become em-brittled if exposed to air while melting.
- Pinpoint accuracy and control. The process provides more precise control of the weld than any other arc welding process because the arc heat and filler metal are independently controlled.
- Good looking welds beads
- For metals of varying thickness including very thin metals (amperage range of 5 to 800, which is the amount of electricity created by the welding machine). The gas tungsten arc welding process is very good for joining thin base metals because of the excellent control of heat input.
- Creates strong joints. It produces top quality welds in almost all metals and alloys used by industry.
- A clean process with a minimal amount of fumes, sparks, spatter and smoke
- High level of visibility when working due to low levels of smoke. Visibility is excellent because no smoke or fumes are produced during welding, and there is no slag or spatter that must be cleaned between passes or on a completed weld.
- Minimal finishing required. In very critical service applications or for very expensive metals or parts, the materials should be carefully cleaned of surface dirt, grease, and oxides before welding.
- Works in any welding position
- TIG welding also has reduced distortion in the weld joint because of the concentrated heat source.
- As in oxyacetylene welding, the heat source and the addition of filler metal can be separately controlled.
- Because the electrode is non-consumable, the process can be used to weld by fusion alone without the addition of filler metal.
Disadvantages
- Brighter UV rays when compared to other welding processes
- Slower process than consumable electrode arc welding processes.
- Takes practice
- More expensive process overall. Expensive welding supplies (vs. other processes) because the arc travel speed and weld metal deposition rates are lower than with some other methods. Inert gases for shielding and tungsten electrode costs add to the total cost of welding compared to other processes. Argon and helium used for shielding the arc are relatively expensive. Equipment costs are greater than that for other processes, such as shielded metal arc welding, which requires less precise controls.
- Not easily portable, best for a welding shop
- Transfer of molten tungsten from the electrode to the weld causes contamination. The resulting tungsten inclusion is hard and brittle.
- Exposure of the hot filler rod to air using improper welding techniques causes weld metal contamination.
Tips
As mentioned, since tungsten welding operates at high temperatures, ideal metals are those that have a low melting point. This includes:
- Aluminum: use on AC output and high-frequency setting. Keep the tungsten from touching the piece being welded to avoid contamination. Conducts heat. Clean aluminum with a wire brush (even if it looks clean) to remove aluminum oxide. Use high heat settings to increase welding speed.
- Magnesium: similar properties to aluminum
- Copper alloys (brass, bronze, copper nickel, copper aluminum, silicon): use DC current with electrode negative
- Stainless steel: requires the use of a filler rod with high chrome component. Use gas lenses for better gas coverage of weld. Keep gas flow at 15 to 20 cfh.
- Mild steel: use rods with deoxidizers. The tungsten electrode should be 2% thoriated. Clean the steel before welding.
If TIG weld cracking occurs preheat the metal to 400 degrees Fahrenheit. This helps with the contraction and expansion of the metals when welding.
 Process-b.jpg)
TIG welding process (10 steps)
- Step 1: Select the electrode
- Step 2: Prepare the electrode by properly grinding it
- Step 3: Insert the tungsten electrode in the electrode holder
- Step 4: Make the recommended settings on the TIG welder as per requirement
- Step 5: Turn on gas cylinders
- Step 6: Clean the work piece surface
- Step 7: Wear safety glasses, helmet, welding coat, etc.
- Step 8: Start welding the work piece
- Step 9: Close the valve of gas cylinder
- Step 10: Turn off welder after welding is completed
References
- Weld Guru
- TWI