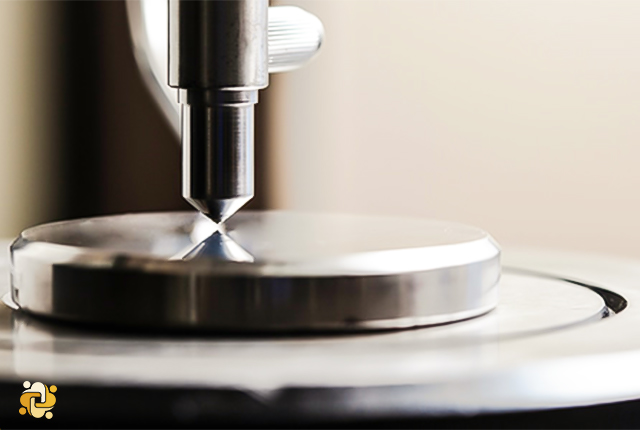
آزمون های مخرب مورد استفاده در فرآیند تایید جوش
۱۴۰۱/۰۹/۰۶ 20:47
مقدمه
آزمون یا تست یکی از اساسی ترین اجزای هر فعالیت مهندسی است. در بسیاری از مراحل فرآیند پیچیده تولید یک ماده مهندسی، تستهای مختلفی برای ارزیابی و صحه گزاری ساخت آن ماده باید انجام بپذیرد. نیاز به این تست ها علاوه بر زمان ساخت، برای زمان در سرویس بودن آن نیز در اغلب موارد ضروری خواهد بود و در نتیجه آن تغییرات احتمالی ایجاد شده در ماده مهندسی، از قبیل خسارت های مربوط به خستگی و خوردگی، مشخص می گردد. بر این اساس انواع آزمون های مورد استفاده را می توان در دو دسته کلی زیر تقسیم بندی کرد:
- آزمون های تعیین خواص مواد و یا قطعات
- آزمون های تعیین درستی مواد و یا قطعات
آزمون های دسته اول عموما از نوع مخرب هستند. به صورتی که برای تعیین خواص ماده یا قطعه مورد نظر، نمونه ای استاندارد تهیه و بر روی آن آزمون انجام می گیرد. بدیهی است که در آزمون مخرب نمونه مورد آزمایش، آسیب می بیند و یا از بین می رود. به عنوان مثال، آزمون کشش یکی از انواع آزمون های مخرب است که نمونه تا حد شکست تحت کشش قرار گرفته و نتایج آن بررسی و مستند می شود.
آزمون های دسته دوم عموما، ماهیت غیر مخرب دارند و برای بررسی وجود عیوب حین سرویس مواد و یا قطعات بدون آسیب یا تخریب آنها، استفاده می شود. در این آزمون ها نمونه برداری ضرورت ندارد، و بررسی ها بر روی قطعه اصلی انجام می شود.
در آزمون های مخرب خواصی از قبیل استحکام کششی، فشاری، برشی در دمای محیط و دیگر دما ها، سفتی، سختی، استحکام ضربه ای، خواص تابع زمان مانند پدیده های خستگی و خزش، مقاومت به اکسایش و خوردگی مورد ارزیابی قرار می گیرد.
در بسیاری از استاندارد های مربوط به تهیه مدارک جوشکاری، برای تأیید یک جوش می توان از تست های مخرب مورد بحث در این مقاله استفاده نمود.
این مقاله به توصیف مختصری در خصوص انواع آزمون های مخرب مورد استفاده در فرآیند تایید جوش می پردازد.
آزمون کشش اتصالات جوش داده شده
برای تعیین استحکام کششی فلز جوش یا اتصال جوش داده شده، می توان بر اساس استاندارد های مورد استفاده، نمونه های آزمون مورد نظر را تهیه کرد. مهمترین آزمون های کشش برای ارزیابی قطعه جوشکاری شده، شامل موارد زیر است:
- آزمون تمام فلز جوش
- آزمون جوش لب به لب عرضی
- آزمون جوش لب به لب طولی
آزمون تمام فلز جوش، میله ای در محور جوش مطابق با استاندارد مورد نظر تهیه می شود که تمام آن از فلز جوش تشکیل گردیده است. این نمونه برای آزمون کشش به آزمایشگاه فرستاده خواهد شد. عموما تنها پیچیدگی این روش ترکیب شدن احتمالی فلز جوش با فلز پایه ذوب شده است.
آزمون جوش لب به لب عرضی، شامل نمونه ای است که خط جوش نسبت به محل گیره های آزمون کشش به صورت عمودی جانمایی شده است.
آزمون جوش لب به لب طولی، به صورتی است که جهت خط جوش نمونه موازی با جهت اعمال نیروی کششی است.
در نهایت آنچه که باید مورد توجه قرار گیرد، نمونه هایی است که بر اساس استاندارد مورد نظر طراح و سازنده تهیه شده است.
آزمون های خمش
از آزمون های خمش برای ارزیابی کیفیت جوش بر حسب داکتیلیته فلز جوش و HAZ و همچنین آزمون های آشکارسازی عیوب جوش به ویژه ذوب ناقص دیواره جانبی، ذوب ناکافی ریشه جوش و نفوذ ناقص اتصال جوش استفاده می شود.
این آزمون ها، به سه گروه تقسیم می شود:
- آزمون خمش آزاد
- آزمون خمش هدایت شده
- آزمون خمش کنترل شده
نمونه های آزمون خمش می توانند به صورت عمود و یا موازی با محور جوش تهیه شوند. نتایج آزمون خمش به صورت های مختلفی بیان می شود:
- درصد ازدیاد طول در فیبر های خارجی نمونه
- شعاع خمش حداقل قبل از تخریب
- زاویه خمش قبل از تخریب
آزمون خمش در مورد تشخیص تردی، آشکار سازی ترک ها یا عیوب شامل عدم ذوب کافی، ناخالصی های سرباره ای بزرگ در جوش، ترک در HAZ موثر و مفید است. البته عموما، ریز ترک ها در این آزمون شناسایی نمی شوند.
آزمایش سختی
معمولا، سختی به خاصیت اجسام در مقابل نفوذ جسم دیگری به سطح آنهاو مقاومت و نفوذناپذیری آنها اطلاق می گردد. رایج ترین آزمایش سختی، حرکت یک جسم نفوذ کننده یا فرورونده به داخل نمونه و ثبت نیروی لازم برای این کار یا اندازه گیری مقدار فرورفتگی در برابر آن است.
متداول ترین نوع آزمایش سختی، نوع ایستای آن است. به صورتی که حفره ای تحت فشار معین در نمونه ایجاد می شود و ابعادش اندازه گیری می شود. گرچه این نوع آزمون برای ارزیابی مقاومت برابر سایش طراحی نشده است، اما عموما موادی که در این آزمون دارای سختی بالاتری اندازه گیری شوند، مقاومت بالاتری در برابر سایش نیز خواهند داشت.
نوع دیگری از آزمایش سختی، آزمون پویای آن است به گونه ای که وزنه یا آونگی آزادانه رها می شود و به سطح نمونه برخورد می کند. این نوع آزمون برای نمونه های دارای سختی بالاتر مناسب است زیرا مواد با این مشخصه، تغییر شکل پلاستیک سطحی بسیار کمی خواهند داشت و اندازه گیری فاصله برگشت وزنه بعد از برخورد را می توان در رابطه ای برای تعیین سختی سطح آن به کار برد.
بسیاری از آلیاژهای فلزی ساختاری همگن ندارند و انجام یکبار آزمون نمی تواند بیانگر خاصیت کلی نمونه باشد. به این دلیل اندازه گیری باید در چندین نوبت انجام بگیرد. به طور معمول، سه آزمون فروروندگی ایستا بیش از بقیه مورد استفاده قرار می گیرند:
- آزمون ویکرز الماسی
- آزمون برینل
- آزمون راکول
آزمایش ضربه و شکست ترد
در جنگ جهانی دوم توجه زیادی به شکست ترد تانکر های T-2 و کشتی های لیبرتی جوشکاری شده، معطوف شد. برخی از این کشتی ها، کاملا به دو قسمت تقسیم شده بودند. بیشتر این شکست ها در هوای سرد زمستان رخ داده بود درست در زمانی که کشتی ها در لنگرگاه ثابت بودند. بررسی ها نشان می داد که فولاد که معمولا نرم است، در شرایط ویژه ای ترد می شود.
برای تعیین تمایل یک ماده به داشتن رفتار ترد، انواع مختلف آزمایش ضربه به کار برده می شود. این نوع آزمایش تفاوت هایی را بین مواد مشخص می کند که در آزمایش کشش قابل مشاهده نیستند.
امروزه تمامی آزمون های ضربه جوش ها با استفاده از نمونه و ماشین نوع چارپی انجام می پذیرد. مزیت این نوع آزمون در این است که آزمون های درجه حرارت پایین تنها با سرد کردن نمونه، امکان پذیر است. در استاندارد های مختلف انواع مختلف نمونه های مورد استفاده در این نوع آزمون، تعیین گردیده است.
آزمون های خستگی
یک قطعه یا سازه ممکن است هنگام کار تحت تأثیر تنش های تناوبی قرار بگیرد. به ندرت اتفاق می افتد که یک قطعه در تمام عمر کاری اش فقط در معرض یک نوع چرخه بارگزاری قرار داشته باشد. دستگاه های متنوعی برای انجام آزمون خستگی طراحی شده اند ولی برای نمونه آزمایش، استانداردی وجود ندارد. نتایج آزمون خستگی معمولا به صورت منحنی های S-logN نمایش داده می شود.
تخریب ناشی از خستگی یکی از متداول ترین انواع خرابی در حین سرویس است که میزان 90 درصد خرابی های قطعات جوشکاری شده را به خود اختصاص می دهد.
آزمون های خستگی برای اندازه گیری تأثیر بارگزاری تناوبی تنش روی اتصال جوشکاری شده طراحی می شوند. بدین منظور میله های آزمون طراحی شده و برخی مواقع سازه های تکمیل شده یا قطعات دستگاه و مقاطع کاملا جوشکاری شده مورد آزمایش قرار می گیرند.