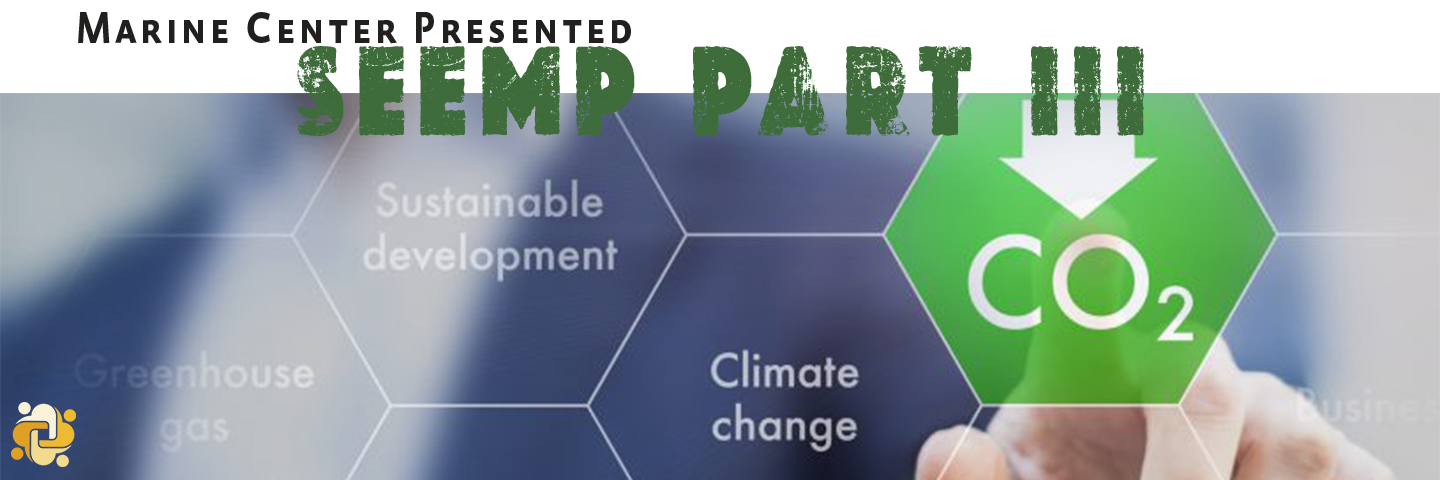
Ship Energy Efficiency Management Plan (SEEMP) PART I
Regulation 26.1 of MARPOL Annex VI requires each ship of 400 gross tonnage and above, subject to Chapter 4 to keep on board a ship specific Ship Energy Efficiency Management Plan (SEEMP). The purpose of Part I of SEEMP is to establish a mechanism for a company and/or a ship to improve the energy efficiency and reduce the carbon intensity of a ship's operation. Preferably, this aspect of the ship-specific SEEMP is linked to a broader corporate energy management policy for the company that owns, operates or controls the ship, recognizing that no two shipping companies are the same, and that ships operate under a wide range of different conditions.
Many companies will already have an environmental management system (EMS) in place under ISO 14001 which contains procedures for selecting the best measures for particular ships and then setting objectives for the measurement of relevant parameters, along with relevant control and feedback features. Monitoring of operational environmental efficiency should therefore be treated as an integral element of broader company management systems.
In addition, many companies already develop, implement and maintain a Safety Management System. In such case, Part I of SEEMP may form part of the ship’s Safety Management System.
Part I of the SEEMP is intended to be a management tool to assist a company in managing the ongoing environmental performance of its ships and as such, it is recommended that a company develops procedures for implementing the plan in a manner which limits any on-board administrative burden to the minimum necessary.
Part I of SEEMP should be developed as a ship-specific plan by the company, and should reflect efforts to improve the energy efficiency and reduce carbon intensity of a ship through four steps:
- planning,
- implementation,
- monitoring,
- self-evaluation and improvement.
 PART I-a.jpg)
These components play a critical role in the continuous cycle to improve ship energy efficiency management and reduce its carbon intensity. With each iteration of the cycle, some elements of Part I will necessarily change while others may remain as before.
At all times safety considerations should be paramount. The trade a ship is engaged in may determine the feasibility of the energy efficiency and carbon intensity reduction measures under consideration. For example, ships that perform services at sea (pipe laying, seismic survey, OSVs, dredgers, etc.) may choose different methods of improving energy efficiency when compared to conventional cargo carriers. The nature of operations and influence of prevailing weather conditions, tides and currents combined with the necessity of maintaining safe operations may require adjustment of general procedures to maintain the efficiency of the operation, for example the ships which are dynamically positioned. The length of a voyage and the need to avoid high risk areas may also be important parameters as well as trade specific safety considerations.
FRAMEWORK AND STRUCTURE OF PART I OF SEEMP
Planning
Planning is the most crucial stage of Part I of SEEMP, in that it primarily determines both the current status of ship energy usage and carbon intensity and the expected improvement of ship energy efficiency and reduction of carbon intensity. Therefore, it is encouraged to devote sufficient time to planning so that the most appropriate, effective and implementable plan can be developed.
Ship-specific measures
Recognizing that there are a variety of options to improve energy efficiency and reduce carbon intensity (e.g. – speed optimization, confirming berth availability and arrival time with port of destination, weather routing, hull maintenance, retrofitting of energy efficiency devices, and use of alternative fuels), the best package of measures for a ship to improve energy efficiency and reduce carbon intensity depends to a great extent upon ship type, cargoes, routes and other factors that should be identified in the first place. These measures should be listed as a package of measures to be implemented, thus providing the overview of the actions to be taken for that ship.
During the planning process, therefore, it is important to determine and understand the ship's current status of energy usage. Part I of SEEMP should identify energy-saving and carbon intensity reducing measures that already have been undertaken, and should determine how effective these measures are in terms of improving energy efficiency and reducing carbon intensity. Part I also should identify what measures can be adopted to further improve the energy efficiency and reduce the carbon intensity of the ship. It should be noted, however, that not all measures can be applied to all ships, or even to the same ship under different operating conditions and that some of them are mutually exclusive. Ideally, initial measures could yield energy (and cost) saving results that then can be reinvested into more difficult or expensive efficiency upgrades identified by Part I.
The improvement of energy efficiency and reduction of carbon intensity of ship operation does not necessarily depend on single ship management only. Rather, it may depend on many stakeholders including ship repair yards, ship-owners, operators, charterers, cargo owners, fuel suppliers, ports and traffic management services. For example, "Just in time" requires good early communication among operators, ports and traffic management services. The better the coordination among such stakeholders, the more improvement can be expected. In most cases, such coordination or total management is better made by a company rather than by a ship. In this sense, it is recommended that a company should also establish an energy efficiency and carbon intensity management plan to improve the performance of its fleet (should it not have one in place already) and make necessary coordination among stakeholders.
For effective and steady implementation of the adopted measures, raising awareness of and providing necessary training for personnel both on shore and on board are an important element. Such human resource development is encouraged and should be considered as an important component of planning as well as a critical element of implementation.
The last part of planning is goal setting
For ships also subject to regulation 28 of MARPOL Annex VI, the goal setting should be consistent with the continuous CII improvements set out by that regulation, and should include the relevant information (The goal setting, in Part I, should be consistent with the requirements of regulation 28 of MARPOL Annex VI and should include the ship's required annual operational CII for the next three years following the updating of the SEEMP).
These ships are also encouraged to consider setting ship-specific goals in addition to the applicable CII requirements that strive for additional energy efficiency improvements and carbon intensity reductions.
For ships or companies not subject to regulation 28, there are no requirements to define a goal and to communicate it to the public, or to be a subject to external inspection, surveys, or audits with respect to the SEEMP. Nevertheless, a meaningful goal should be defined to serve as a signal on a company’s commitment to improve the energy efficiency and carbon intensity of the ship. The goal can be set using different indicators, including the annual fuel consumption, Annual Efficiency Ratio (AER), cgDIST, Energy Efficiency Operational Indicator (EEOI) or other Carbon Intensity Indicators (CIIs). In all cases, the goal should be measurable and easy to understand.
Click on the image below for CII Calculation.
 PART I-b.jpg)
Implementation
After a ship and a company identify the energy efficiency and carbon intensity measures to be implemented, it is essential to establish a system for their implementation. This is done by developing the procedures for energy management, defining tasks associated with those procedures, and assigning those tasks to responsible personnel. The implementation system should include procedures to ensure execution of measures and specify defined levels of authority and lines of communication. Also, it should include procedures for internal audits and management review, where relevant. In sum, Part I of SEEMP should describe how each measure should be implemented and who the responsible person(s) is (are). The implementation period (start and end dates) of each selected measure should be indicated. The development of such an implementation system can be considered as a part of planning, and therefore may be completed at the planning stage.
After a ship and a company identify the energy efficiency and carbon intensity measures to be implemented, it is essential to establish a system for their implementation. This is done by developing the procedures for energy management, defining tasks associated with those procedures, and assigning those tasks to responsible personnel. The implementation system should include procedures to ensure execution of measures and specify defined levels of authority and lines of communication. Also, it should include procedures for internal audits and management review, where relevant. In sum, Part I of SEEMP should describe how each measure should be implemented and who the responsible person(s) is (are). The implementation period (start and end dates) of each selected measure should be indicated. The development of such an implementation system can be considered as a part of planning, and therefore may be completed at the planning stage.
The planned measures should be carried out in accordance with the predetermined implementation system. Record-keeping for the implementation of each measure is beneficial for self-evaluation at a later stage and should be encouraged. If any identified measure cannot be implemented for any reason(s), the reason(s) should be recorded for internal use. It is recommended that events and operational conditions outside the control of the ship’s crew (for example, waiting for berths, extended port dwell times, operation in severe adverse weather) which may affect the ships rating, be documented.
Monitoring
The energy efficiency of a ship should be monitored quantitatively. This should be done by an established method, preferably by an international standard. In many cases, the monitoring tool should target the goal indicator set out (e.g., AER, cgDIST, EEOI, or other CIIs as agreed by the Organization).
If a quantitative goal is not defined for a ship, a quantitative performance indicator developed by the Organization (e.g., AER, EEOI, CII) or another internationally established tool should be selected. A ship subject to regulation 28 is likely to use the CII as its monitoring tool.
If used, these CIIs should be calculated in accordance with the Guidelines developed by the Organization, adjusted, as necessary, to a specific ship and trade. Ships subject to regulation 28 may use other measurement tools in addition to the CII, if convenient and/or beneficial for a ship or a company. In the case where other monitoring tools are used, the reason for the use of the tool and the method of monitoring should be clarified at the planning stage.
It is highly advised to conduct monitoring at regular intervals for checking consistency of data and verification assistance. The ship’s fuel oil consumption should be monitored using daily reporting, such as noon reports, or higher frequency data.
It should be noted that whatever measurement tools are used, continuous and consistent and reliable data collection is the foundation of monitoring. To allow for meaningful and consistent monitoring, a monitoring system, including the procedures for collecting data and the assignment of responsible personnel, should be developed. The development of such a system can be considered as a part of planning, and therefore should be completed at the planning stage.
It should be noted that, in order to avoid unnecessary administrative burdens on ships' staff, monitoring should be carried out as much as possible by shore staff when the data can be automatically transferred, utilizing data obtained from existing required records such as the official and engineering log-books and oil record books, etc. Additional data could be obtained as appropriate.
When a ship diverts from its scheduled passage to engage in search and rescue operations, and for which emissions are excluded pursuant to regulation 3, it is recommended that data obtained during such operations is not used in ship energy efficiency monitoring, and that such data should be recorded separately.
Self-evaluation and improvement
Self-evaluation and improvement is the final phase of the management cycle. This phase should produce meaningful feedback for the coming first stage, i.e. planning stage of the next improvement cycle.
The purpose of self-evaluation is to:
- Evaluate the effectiveness of the planned measures and their implementation;
- Deepen the understanding of the overall characteristics of the ship's operation such as what types of measures can/cannot function effectively, and how and/or why;
- Comprehend the trend of the efficiency improvement of that ship; and
- Develop the improved management plan for the next cycle through identification of further opportunities for improving energy efficiency and reducing carbon intensity.
For this process, procedures for self-evaluation of the ship energy efficiency management plan should be developed. Furthermore, self-evaluation should be implemented periodically by using data collected through monitoring. In addition, it is recommended to invest time in identifying the cause-and-effect of the performance during the evaluated period so lessons learned can be taken into account when revising and improving the next stage of the ship’s energy efficiency management plan.
GUIDANCE ON BEST PRACTICES FOR FUEL-EFFICIENT OPERATION OF SHIPS
The search for energy efficiency and carbon intensity improvement across the entire transport chain takes responsibility beyond what can be delivered by the company alone. A list of all the possible stakeholders in the efficiency of a single voyage is long; obvious parties are designers, shipyards and engine manufacturers for the characteristics of the ship, and charterers, fuel suppliers, ports and vessel traffic management services, etc., for the specific voyage. All involved parties should consider the inclusion of efficiency measures in their operations both individually and collectively.
Fuel-efficient operations
Improved voyage planning
The optimum route and improved efficiency can be achieved through the careful planning and execution of voyages. Thorough voyage planning needs time, but a number of software tools are available to assist in voyage planning.
The Guidelines for voyage planning, adopted by resolution A.893 (21), provide essential guidance for the ship's crew and voyage planners.
The aforementioned resolution can be viewed here.
Weather routing
Weather routing has a high potential for efficiency savings on specific routes. It is commercially available for all types of ship and for many trade areas.
Just in-time
Good early communication with the next port should be an aim in order to give maximum notice of berth availability and facilitate the use of optimum speed where port operational procedures support this approach.
Optimized port operation could involve a change in procedures involving different ship handling arrangements in ports. Port authorities should be encouraged to maximize efficiency and minimize delay.
 PART I-c.jpg)
Speed optimization
Speed optimization can produce significant savings. However, optimum speed means the speed at which the fuel used per ton mile is at a minimum level for that voyage. It does not mean minimum speed; in fact, sailing at less than optimum speed will consume more fuel rather than less. Reference should be made to the engine manufacturer's power/consumption curve and the ship's propeller curve. Possible adverse consequences of slow speed operation may include increased vibration and problems with soot deposits in combustion chambers and exhaust systems. These possible consequences should be taken into account. For LNG carriers speed optimization means, quite often, a higher speed at the start of laden passages to control tanks pressure and at the end of ballast passages to use the operational LNG quantity needed for cargo tank cooling in propulsion instead of wasting in GCU or condenser steam dump. Charterers are generally aware of the improved efficiency of this speed pattern.
As part of the speed optimization process, due account may need to be taken of the need to coordinate arrival times with the availability of loading/discharge berths, etc. The number of ships engaged in a particular trade route may need to be taken into account when considering speed optimization.
A gradual increase in speed when leaving a port or estuary whilst keeping the engine load within certain limits may help to reduce fuel consumption.
It is recognized that under many charter parties the speed of the ships is determined by the charterer and not the operator. Efforts should be made when agreeing charter party terms to encourage the ship to operate at optimum speed in order to maximize energy efficiency.
Optimized shaft power
Operation at constant shaft RPM can be more efficient than continuously adjusting speed through engine power. The use of automated engine management systems to control speed rather than relying on human intervention may be beneficial.
When optimizing shaft power, due attention should be given to overall power system efficiency. For example, in some cases reducing load or shaft speed below the minimum necessary to operate energy recovery systems and shaft generators may increase overall emissions.
Optimized ship handling
Optimum trim
Most ships are designed to carry a designated amount of cargo at a certain speed for a certain fuel consumption. This implies the specification of set trim conditions. Loaded or unloaded, trim has a significant influence on the resistance of the ship through the water and optimizing trim can deliver significant fuel savings. For any given draft there is a trim condition that gives minimum resistance. In some ships, it is possible to assess optimum trim conditions for fuel efficiency continuously throughout the voyage. Design or safety factors may preclude full use of trim optimization.
Optimum ballast
Ballast should be adjusted taking into consideration the requirements to meet optimum trim and steering conditions and optimum ballast conditions achieved through good cargo planning.
When determining the optimum ballast conditions, the limits, conditions and ballast management arrangements set out in the ship's Ballast Water Management Plan are to be observed for that ship.
Ballast conditions have a significant impact on steering conditions and autopilot settings and it needs to be noted that less ballast water does not necessarily mean improved energy efficiency.
Optimum propeller and propeller inflow considerations
Selection of the propeller is normally determined at the design and construction stage of a ship's life but new developments in propeller design have made it possible for retrofitting of later designs to deliver greater fuel economy. Whilst it is certainly for consideration, the propeller is but one part of the propulsion train and a change of propeller in isolation may have no effect on efficiency and may even increase fuel consumption.
Improvements to the water inflow to the propeller using arrangements such as fins and/or nozzles could increase propulsive efficiency power and hence reduce fuel consumption.
Optimum use of rudder and heading control systems (autopilots)
There have been large improvements in automated heading and steering control systems technology. Whilst originally developed to make the bridge team more effective, modern autopilots can achieve much more. An integrated Navigation and Command System can achieve significant fuel savings by simply reducing the distance sailed "off track". The principle is simple; better course control through less frequent and smaller corrections will minimize losses due to rudder resistance. Retrofitting of a more efficient autopilot to existing ships could be considered.
During approaches to ports and pilot stations the autopilot cannot always be used efficiently as the rudder has to respond quickly to given commands. Furthermore, at certain stages of the voyage it may have to be deactivated or very carefully adjusted, i.e. heavy weather and approaches to ports.
Consideration may be given to the retrofitting of improved rudder blade design (e.g. "twist-flow" rudder).
Hull maintenance
Docking intervals should be integrated with the company's ongoing assessment of ship performance. Hull resistance can be optimized by new technology-coating systems, possibly in combination with cleaning intervals. Regular in-water inspection of the condition of the hull is recommended.
Propeller cleaning and polishing or even appropriate coating may significantly increase fuel efficiency. The need for ships to maintain efficiency through in-water hull cleaning should be recognized and facilitated by port States.
Consideration may be given to the possibility of timely full removal and replacement of underwater paint systems to avoid the increased hull roughness caused by repeated spot blasting and repairs over multiple dockings.
Generally, the smoother the hull, the better the fuel efficiency.
 PART I-d.jpg)
Propulsion system
Marine diesel engines have a very high thermal efficiency (~50%). This excellent performance is only exceeded by fuel cell technology with an average thermal efficiency of 60%. This is due to the systematic minimization of heat and mechanical loss. In particular, the new breed of electronic controlled engines can provide efficiency gains. However, specific training for relevant staff may need to be considered to maximize the benefits.
Propulsion system maintenance
Maintenance in accordance with manufacturers' instructions in the company's planned maintenance schedule will also maintain efficiency. The use of engine condition monitoring can be a useful tool to maintain high efficiency.
Additional means to improve engine efficiency might include use of fuel additives; adjustment of cylinder lubrication oil consumption; valve improvements; torque analysis; and automated engine monitoring systems.
Waste heat recovery
Waste heat recovery systems use thermal heat losses from the exhaust gas for either electricity generation, heating or additional propulsion with a shaft power take in.
It may not be possible to retrofit such systems into existing ships. However, they may be a beneficial option for new ships. Shipbuilders should be encouraged to incorporate new technology into their designs.
Improved fleet management
Better utilization of fleet capacity can often be achieved by improvements in fleet planning. For example, it may be possible to avoid or reduce long ballast voyages through improved fleet planning. There is opportunity here for charterers to promote efficiency. This can be closely related to the concept of "just in time" arrivals.
Efficiency, reliability and maintenance-oriented data sharing within a company can be used to promote best practice among ships within a company and should be actively encouraged.
Improved cargo handling
Cargo handling is in most cases under the control of the port or terminal operators and optimum solutions matched to ship and port or terminal requirements should be explored. However, in cases where ships use their own cargo handling equipment (e.g., cargo cranes, self-unloading booms, cargo pumps (tankers)) procedures should be in place to efficiently utilize the energy produced from any additional generators required to operate the equipment.
Energy management
A review of electrical services on board can reveal the potential for unexpected efficiency gains. However, care should be taken to avoid the creation of new safety hazards when turning off electrical services (e.g. lighting). Thermal insulation is an obvious means of saving energy.
Optimization of reefer container stowage locations may be beneficial in reducing the effect of heat transfer from compressor units. This might be combined as appropriate with cargo tank heating, ventilation, etc. The use of water-cooled reefer plant with lower energy consumption might also be considered.
Fuel type
The use of emerging alternative fuels may be considered as a CO2 reduction method, but availability will often determine the applicability.
Other measures
Development of computer software for the calculation of current fuel consumption, for the establishment of an emissions "footprint," to optimize operations, and the establishment of goals for improvement and tracking of progress may be considered.
Renewable energy sources, such as solar (or photovoltaic) cell technology, have improved enormously in the recent years and should be considered for on-board application.
In some ports shore power may be available for some ships but this is generally aimed at improving air quality in the port area. If the shore-based power source is carbon efficient, there may be a net efficiency benefit. Ships may consider using onshore power if available.
Even wind assisted propulsion may be worthy of consideration. Various systems are available for retrofit, including Flettner Rotors, wing sails and aerofoil kites.
Efforts could be made to source fuel of improved quality in order to minimize the amount of fuel required to provide a given power output.
Compatibility of measures
These Guidelines indicate a wide variety of possibilities for energy efficiency improvements for the existing fleet. While there are many options available, they are not necessarily cumulative, are often area and trade dependent and likely to require the agreement and support of a number of different stakeholders if they are to be utilized most effectively.
Age and operational service life of a ship
All measures identified in this document as applied to Part I of the SEEMP, are potentially cost-effective in case of high oil prices. The financial feasibility of a specific energy efficiency enhancement can be evaluated by various means. One way would be to estimate the Return of Investment (ROI) time. However, while measures with lower ROI may have the lowest cost, this does not guarantee the best results in energy efficiency performance improvement. Clearly, this equation is heavily influenced by the remaining service life of a ship and the cost of fuel.
Trade and sailing area
The feasibility of many of the measures described in this guidance will be dependent on the trade and sailing area of the ship. Sometimes ships will change their trade areas as a result of a change in chartering requirements, but this cannot be taken as a general assumption. For example, certain types of wind-enhanced power sources might not be feasible for short sea shipping as these ships generally sail in areas with high traffic densities or in restricted waterways. Air draft limitations may also affect the feasibility of wind assistance technology and certain other emission reduction measures. Another aspect is that the world's oceans and seas each have characteristic conditions and so ships designed for specific routes and trades may not obtain the same energy efficiency benefits by adopting the same measures or combination of measures as other ships that operate in different areas. It is also likely that some measures will have a greater or lesser effect in different sailing areas.
The trade a ship is engaged in may also determine the feasibility of the efficiency measures under consideration. For example, ships that perform services at sea (pipe laying, seismic survey, OSVs, dredgers, etc.) may choose different methods of improving energy efficiency when compared to conventional cargo carriers. The length of voyage may also be an important parameter as may trade specific safety considerations. The pathway to the most efficient combination of measures will be unique to each vessel within each shipping company.
Environmental conditions and the nature of cargo carried also varies between regions. For example, some routes may carry greater volumes of goods requiring careful temperature conditioning, or some transit regions may be subject to frequent severe adverse weather conditions. This may lead to an increase of emissions of ships serving those routes and regions.
SAMPLE FORM OF SHIP MANAGEMENT PLAN TO IMPROVE ENERGY EFFICIENCY (PART I OF THE SEEMP)